The various regulatory agencies have expectations that pharmaceutical manufacturers will demonstrate control over their manufacturing equipment. The FDA’s findings of deficiencies concerning equipment validation indicate the agencies expect definitive evidence that the equipment qualification and validation schedules of a facility will satisfactorily control their manufacturing processes. Examples of FDA form 483 findings for equipment qualification and validation indicate deficiencies in many of these studies.
The cost of non-compliance is therefore more than that of compliance. Are you in compliance with the FDA regulations for equipment qualification and validation in your manufacturing facility?
In this webinar you will learn the different global agencies expectations of equipment qualification along with the development of a sound process validation program in order to develop and implement bulletproof solutions that are accepted, effective, and efficient. Through case study analysis we will examine best practices to provide thoughts and ideas to develop or improve the performance of your current system. Additionally, case studies will explore how your management practices of your equipment qualification/ validation and process validation programs can help or hurt your legal liability and the legal issues that arise from non-conformance with regulators and Auditors.
Session 1:
- Regulatory requirements and expectations for Equipment Qualification
- Europe
- FDA
- Global harmonization and expectations
- Management of Documents, Documents required
- Validation Policy
- Validation Master Plan (VMP)
- Documents Equipment Qualification
- SOPs
- Responsibilities
- Validation Team
- Presumption for Qualification/Validation
Session 2:
- General Aspects of Qualification
- Qualification Phases, DQ, IQ, OQ, PQ
- Qualification of existing systems and equipment
- Requalification/Validation
- Performance Qualification
- SOPs
- Writing a qualification protocol, content
- Executing a qualification
- Tests, and data
- Documents
- Writing a qualification final report
- Questions
Session 3:
- Performance of a Process Validation
- SOPs
- Writing a Process validation protocol
- Guidelines on validating analytical methods
- Content and execution
- SOPs
- Writing the validation plan
- Methodology and performance
- Report writing for method validation
- Presumption for validation
- Support of Equipment Qualification and Process Validation
- Quality Management System
- Risk Analysis
- Calibration/Maintenance
- Change Control
- Auditing equipment qualification and process validation
- External Equipment Qualification and process Validation
- Contract Manufacturer
- Qualification/Validation by a supplier
- Review of FDA warning letters
- Case Study Exercise from current FDA Warning Letters
- Theoretical Case exercises
- Questions
Areas Covered in the Session :
- Understand what the global expectations are for equipment qualification and validation.
- Understand the documents required for equipment qualification and process validation and how to manage documents appropriately.
- Understand and know how to write and maintain a Validation Master Plan.
- Write and execute sound protocols for equipment qualification (IQ, OQ, PQ) and process validation.
- Qualify already existing systems and re-qualification
- Be able to collect data, conduct tests, and obtain all necessary documents.
- Understand the different types of validation.
- Understand Performance Validation.
- Know the guidelines on validating analytical methods and processes.
- Support equipment qualification and validation through the quality management system, risk analysis, calibration and maintenance, and change control.
- Understand and know the principles of auditing the equipment qualification and validation.
- Understand external qualification and validation from a contract manufacturer, and qualification and validation by a supplier.
- To investigate true root causes of problems and to evaluate and prioritize solutions
- Problem solving methods to help you asses which is best for your situation
- Develop successful implementation plans
- Perform risk assessments effectively
Who Should Attend:
This is a practical webinar designed to provide pharmaceutical, bio-pharmaceutical, biologics and medical device professionals with the information and tools they require to prepare for and manage an FDA inspection. The course is ideal for Managers, Directors, and Vice Presidents of Regulatory Affairs and Quality Assurance.
- Quality Assurance Departments
- Engineering Departments
- Regulatory Affairs Departments
- Manufacturing Departments
- Validation Departments
- Operations Departments
Course Director: JEFF KASOFF
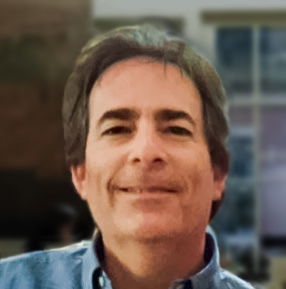 | Jeff Kasoff, RAC, CMQ/OE, LBB, is the Principal at Lean to Quality, LLC. He has more than 30 years in Quality and Regulatory management. Over that time, Jeff has implemented and overseen quality system operations and assured compliance, at all sizes of company, from startup to more than $100 million in revenue. This multi-faceted experience makes Jeff uniquely qualified to address compliance issues across the entire range of company sizes.
Jeff has also been primary liaison with FDA inspectors and notified body auditors, giving him first-hand experience with the most common issues surfaced by regulatory agencies. Jeff has the following certifications: Manager of Quality and Organizational Excellence certification from ASQ, Regulatory Affairs Certification from RAPS, and Lean Black Belt from IIE.
|
|
|
|