Each drug product may be unique due to different components, and this is a known fact. The chemical and physical properties of active pharmaceutical Ingredients (APIs), manufacturing methods and procedures, the excipients, formulations, storage conditions, containers and closers and the stability of the product, etc. make them all the more unique. In pharmaceutical industry, we are required to establish requirements for the expiration and stability on a drug product. The requirements are to assure that the date is appropriate as required by the current good manufacturing practice (CGMP) for finished pharmaceuticals.
This conference is intended to discuss regulatory requirements and good practices to establish a product stability program. In particular, you will know how to present FDA-compliant practices in adequately implementing regulatory requirements for expiration dating and stability testing program depending upon product types.
Why You Should Attend:
Within 60 minutes, you will know why should firms consider and implement the good practices, and remain compliant to recommendations of FDA, so that they can avoid FDA enforcement actions proactively with much awareness. Join the session to know the current view and perspectives of FDA on the product stability testing program.
This product stability testing webinar will explain, in detail, the requirements of the FDA’s drug stability guidelines that are stipulated for drug products and how to design a product stability testing plan that can be applied to new or modified products in the pharmaceutical, biotechnology and medical device industries.
Areas Covered in the Session :
- Introduction of a Stability Testing Plan and Program
- Applicable Regulation and Requirements
- General Stability Considerations Applicable to a New Product (i.e. Potency)
- Storage Conditions
- Shelf Life Duration of Studies and Expiration Dates
- Container Closure Requirements
- Sample Size
- Sampling Plan
- Handling and Analysis of Samples
- Stability Schedule (Suggested Schedules for Conducting Stability Studies)
- Pre-approval and Post Approval Studies
- Stability Tests
- Reformulated Products
- Accelerated Temperature Studies
- Test Schedule Information
- Suggested Time Points and Expiration Dates Based on Testing Time Points
- Solid Dosage Forms Suggested Test Schedule
- Liquid and Semi-solid Types Products Suggested Test Schedule
- Reconstituted Products Suggested Test Schedule
- Temperatures of Studies Based on the Product Type
- Room Temperature Studies
- Elevated Temperature
- Refrigeration
- Freezing Temperature
- Specíal Humidity Considerations
- Analytical Testing Considerations
- Quality Control Release Assays and Methods
- Criticality of the Choice of Test that are Stability Indicators
- Choice of Methods with Meaningful Data or Stability Indicator
- Method Attributes
- Stability Testing Protocol Design
- How to Design a Protocol and a Report
- Stability Testing Data Management and Trending
- Trending Data
- Expiration Dating Extrapolation Using Data
- Manual versus Automated Data Management
- Advantages and Disadvantages
You will also get answers to the following tough questions:
- For a medical device that has storage label of 15-30°C; Are stability studies at 15°C and 30°C or 25°C study sufficient?
- For a reconstitution study; product has an assigned expiration of 24 months; do I need to do reconstitution at 12 months (6, hours, 12 hours and 24 hours) and at 24 months (6, hours, 12 hours and 24 hours)?
- What is the accelerated storage for a product with real time storage of -20°C±5C?
- Is it an industry’s practice to do study one year past expiration?
- If the regression predicts failure before product expiration, what is the next step to do in stability?
Who Should Attend:
- Compliance Departments
- Regulatory Affairs Departments
- Clinical Affairs Professionals
- Quality Assurance Departments
- Laboratory Departments
- R&D Departments
- Consultants
- Contractors/Subcontractors
- Other professionals interested in this topic
Course Director: DR. DAVID LIM
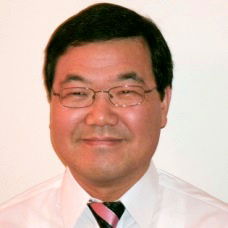 | Dr. David Lim, Ph.D., RAC, ASQ-CQA. Dr. Lim is President and Principal of Regulatory Doctor (www.RegulatoryDoctor.us). As a leading industry speaker, Dr. Lim frequently presents global regulatory and quality compliance topics in various forums and meetings. Recently, Dr. Lim developed 510(k) templates ready for use compliant with e-Copy and RTA policy. In addition, Dr. Lim developed FDA inspection checklists for drug and medical device manufacturers based on his analysis of FDA inspectional observations cited in 483s for the past eight years. Dr. Lim provides his feedback to regulatory agency (e.g., US FDA) through public comments and also served as a panel member during the FDA’s transparency public meeting in 2009.
Dr. Lim contributes to the Regulatory Affairs Professional Society (RAPS) as an author and speaker. Dr. Lim leads and directs all research projects including pharmacovigilance, medical device reporting, recalls and patient safety signals being conducted at the Regulatory Doctor. Dr. Lim currently serves as a member of the Advisory Board for Inspection Insider published by FDA News.
|
|
|
|