Calibration (accuracy) has been traditionally required by ISO 9001, but measurement systems analysis (precision) has not – although it has been an element of the automotive standard IATF 16949 ever since the latter was QS 9000. Accuracy and precision are both, however, necessary to obtain reliable measurements of critical to quality (CTQ) characteristics. Attendees will learn the implications of measurement systems analysis (MSA) with regard to outgoing quality, estimation of process performance indices, and statistical process control, and how to perform and assess a MSA.
Areas Covered in the Session :
- Know the difference between accuracy, as ensured by calibration, and precision, as assessed from a MSA.
- Know how gage variation, a function of repeatability and reproducibility (R&R, alternatively equipment variation and appraiser variation respectively), affects outgoing quality, process performance estimation, and statistical process control.
- The chance of accepting nonconforming work, and rejecting good work, increases near the specification limit(s).
- If gage variation is built into the estimate of process variation, the estimated process performance index will be lower.
- Gage variation is included in the estimate of variation for statistical process control, which means the control limits will be wider and less able to detect genuine process shifts. The false alarm rate will not, however, increase.
- Know the components of gage variation (repeatability and reproducibility), and how to estimate them from data.
- Basic directions are provided for StatGraphics and Minitab, and the handout adds instructions for Microsoft Excel.
- Know the recognized methods for gage studies, including number of parts, number of inspectors, measurements per part, and also the need to randomize the order in which the parts are measured.
- Know potential remedies for non-capable gages, including guard banding (tightening the acceptance limits to protect the customer from nonconforming work, at the expense of rejecting some borderline acceptable product).
Attendees will also receive an Excel spreadsheet with the d*2 factors that are required for the average and range method. These appear in some references that are named in the handout, but they are not as widely available as the traditional control chart factors.
Who Should Attend:
- Quality Departments
- Manufacturing Departments
- Engineering Departments
- Production Departments
- Quality Technicians and Inspectors
- Everyone with responsibility for dimensional measurements
Course Director: WILLIAM LEVINSON
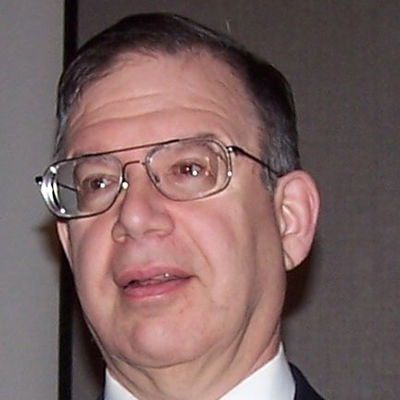 | William (Bill) A. Levinson, P.E., is the principal of Levinson Productivity Systems, P.C. He is an ASQ Fellow, Certified Quality Engineer, Quality Auditor, Quality Manager, Reliability Engineer, and Six Sigma Black Belt. He holds degrees in chemistry and chemical engineering from Pennsylvania State and Cornell Universities, and night school degrees in business administration and applied statistics from Union College, and he has given presentations at the ASQ World Conference, TOC World 2004, and other national conferences on productivity and quality.
Mr. Levinson is also the author of several books on quality, productivity, and management. Henry Ford’s Lean Vision is a comprehensive overview of the lean manufacturing and organizational management methods that Ford employed to achieve unprecedented bottom line results, and Beyond the Theory of Constraints describes how Ford’s elimination of variation from material transfer and processing times allowed him to come close to running a balanced factory at full capacity. Statistical Process Control for Real-World Applications shows what to do when the process doesn’t conform to the traditional bell curve assumption.
|
|
|
|