Process capability reflects the ability of a manufacturing process to meet specifications, and customers often request capability studies for this reason. This presentation will show how to perform a capability study, including not only the calculation procedure but also how to test the data for distributional assumptions. This is important because the normal distribution (bell curve) is far more common in textbooks than it is in the real world, and failure to use the correct distribution can result in an estimate of the nonconforming fraction (defects per million opportunities) that is off by orders of magnitude. Generally accepted and off the shelf techniques are however available for handling non-normal distributions.
Areas Covered in the Session :
- Understand the process capability index (Cp) and process performance index (Pp) as ratios of the specification width to the process variation. Recognize that a non-capable process is similar to a smoothbore musket, which will often miss the target regardless of how well it is centered on the bulls-eye (nominal). A Six Sigma process will on the other hand miss only twice out of every billion opportunities if it is centered on the nominal.
- Know that Cp (and the related Cpk metric) reflects short-term variation, while Pp and Ppk reflect long-term variation. If the rational subgroup (sample) is selected properly, it will reflect all the variation sources, and the two measurements will be roughly equal. If the sample reflects only short-term variation, then Cp will be larger than Pp, and statistical process control charts may also be dysfunctional because the control limits will be too tight.
- Know how to test the data for non-normal distributions, and apply off-the-shelf methods to calculate meaningful and accurate process performance indices. Be sure to create a histogram and a probability plot, and perform quantitative tests for goodness of fit. These tests can also be performed for most non-normal distributions.
- Know how to perform a capability study. This includes not only the calculations, but also the need to keep a control chart to reveal the presence of special or assignable cause variation. A good capability study relies on the assumption that only common cause variation is present.
Who Should Attend:
- Quality Departments
- Manufacturing Departments
- Engineering Departments
- Production Departments
- Quality Technicians and Inspectors
Course Director: WILLIAM LEVINSON
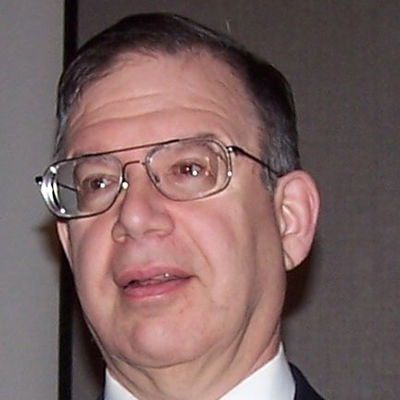 | William (Bill) A. Levinson, P.E., is the principal of Levinson Productivity Systems, P.C. He is an ASQ Fellow, Certified Quality Engineer, Quality Auditor, Quality Manager, Reliability Engineer, and Six Sigma Black Belt. He holds degrees in chemistry and chemical engineering from Pennsylvania State and Cornell Universities, and night school degrees in business administration and applied statistics from Union College, and he has given presentations at the ASQ World Conference, TOC World 2004, and other national conferences on productivity and quality.
Mr. Levinson is also the author of several books on quality, productivity, and management. Henry Ford’s Lean Vision is a comprehensive overview of the lean manufacturing and organizational management methods that Ford employed to achieve unprecedented bottom line results, and Beyond the Theory of Constraints describes how Ford’s elimination of variation from material transfer and processing times allowed him to come close to running a balanced factory at full capacity. Statistical Process Control for Real-World Applications shows what to do when the process doesn’t conform to the traditional bell curve assumption.
|
|
|
|