Every company wants to improve the quality of their products. Attempts to improve product quality need to be structured in such a way that they have a reasonable chance of success and the cost/benefit ratio is appropriate. The most successful method available for such endeavors is called SPC (Statistical Process Control). SPC can also be used to meet ISO requirements for “continual improvement” as well as FDA requirements to “control and monitor production processes”. SPC is a statistical tool that objectively identifies when it is worthwhile to perform a formal investigation of manufacturing variation, in order to identify and reduce its cause. SPC continually adjusts its sensitivity in order to ensure that such investigations are performed only when there is a reasonable chance of identifying causes of variation. SPC also provides information that can be used to estimate what % of items is being produced “in specification”.
Process capability studies are necessary to evaluate the ability of the process to meet specifications. They determine of the process is on target and if the process spread is acceptable. This talk will cover calculation of process capability indices, impact of sample size, confidence intervals and capability analysis of multi-modal and non-normal data. This webinar is valuable for understanding how process capability studies can be used to validate and represent your process. Identifying the correct methods and sample size will save time and money.
Areas Covered in the Session :
- Definition of relevant terms
- Types of control charts
- Calculation of control limits for an XbarR chart
- Rules for detecting “out of control”
- Process Capability Indices (Cp, Cpk, Pp, Ppk)
- Mathematical understanding of Cp/Cpk & Pp/Ppk
- Basic variation and statistics understanding
- Knowledge of why both Cp/Cpk & Pp/Ppk are needed
- Practical application of capability indices
- Common pitfalls and misunderstanding
- Confidence/Reliability Calculation
- SPC Program implementation Recommendations
Who Should Attend:
- Quality Assurance Departments
- Quality Control Departments
- Manufacturing Departments
- Engineering Departments
- Production Departments
- Operations Departments
- Quality Technicians and Inspectors
- Process Engineers
- R&D Engineers
- Design Engineers
- Everyone involved in implementing SPC and who need to use capability indices
Course Director: HITENDRAKUMAR SHAH
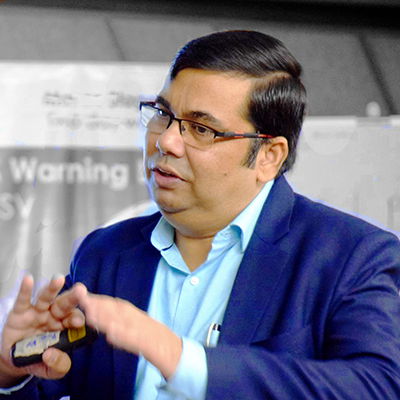 | HitendraKumar Shah is a renowned Quality oriented professional with over 20 years of experience in Quality Assurance and Quality Control. During this period, he has been actively involved in process control, Finished product release, Investigations, product recalls and other quality notifications. He has helped numerous companies in ensuring CAPA implementation & effectiveness, Quality system review and reporting, Supplier audit, GMP training, risk assessment and validation activities. His Key Competencies are but not limited to Quality Compliance, Vendor Audit, data integrity, Risk assessment, Qualification & validation, Review and finalization of technical agreements. He is a popular figure on social media for his effective and easily understandable training bites.
|
|
|
|