In many companies, deviation/non-conformance investigations are often criticized for the lack of a robust root cause analysis. Proper root cause can help a company in many ways.
Root cause analysis helps identify what, how and why something happened, thus preventing recurrence. Root causes are underlying, are reasonably identifiable, can be controlled by management and allow for generation of recommendations. The process involves data collection; cause charting, root cause identification and recommendation generation and implementation.
Why You Should Attend:
If you have reoccurring problems showing up in your quality systems, your Quality system is not effective and you have not performed an in-depth root cause analysis to be able to detect through proper problem solving tools and quality data sources, the true root cause of your problem. Unless you can get to the true root cause of a failure, nonconformity, defect or other undesirable situation, your Quality System will not be successful. Historically, 483s in the pharmaceutical industry related to CAPAs, are due to lack of inadequate root cause investigations, among other factors.
Areas Covered in the Session :
- Know what to do when problems occur
- Define, validate and decide if the problem should be solved
- Use a team approach and understand team dynamics
- Take appropriate interim actions
- Choose the most appropriate RCA methods for the situation
- Determine and implement the best sustainable solution
Who Should Attend:
- Site Quality Operations Managers
- Quality Departments
- Manufacturing Departments
- Plant Managers and Supervisors
- Regulatory Affairs Departments
Course Director: DANIELLE DELUCY
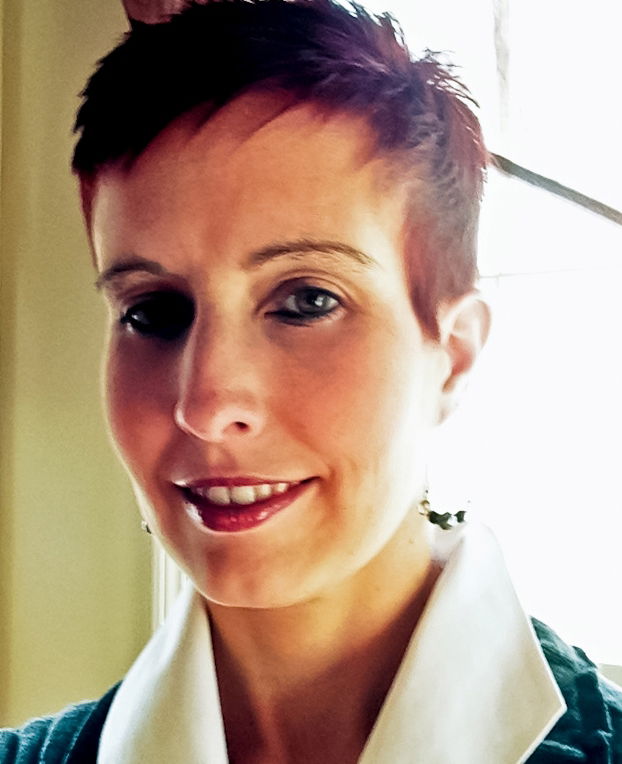 | Danielle DeLucy, MS, is owner of ASA Training and Consulting, LLC which provides Pharmaceutical and Biologics based companies with training and quality systems assistance in order to meet Regulatory compliance.
Prior to this role, Danielle has been in the industry for 15 years serving in numerous Quality Management Roles, such as the Director of Product Quality, the oversight of Sterility Assurance practices and provided QA oversight of numerous filling and packaging operations.
Danielle began her QA career as a Quality Control Pharmaceutical Microbiologist at a contract laboratory where she performed various tests for their clients. In the years after, she has held positions in the Quality management arena while increasing her responsibility. She has helped to lead many Regulatory Health Inspections and was instrumental in the coaching process of her peers prior to any inspection.
Currently, Danielle assists companies who are faced with warning letters, consent decrees and those wishing to improve compliance establish more robust quality systems so that the company can succeed.
|
|
|
|