Almost all manufacturing and development companies perform at least some process validation studies, but it is difficult to decide how many Lots to include in the study and how large the Sample per Lot should be.
This webinar provides a “statistical” justification and method for determining Sample Sizes, and a statistical justification for using only 3 Lots (which is the typical number, especially in industries regulated by the FDA).
Those justifications can then be documented in Protocols or regulatory submissions, or can be given to regulatory auditors who may ask for them during onsite audits at your company. Thus, this webinar is designed to help you avoid regulatory delays in product approvals and to prevent an auditor from issuing you a nonconformity.
This webinar does not address clinical trials, nor bulk-solution processes. It applies to unitized products such as pills, drug-filled syringes, medical devices, and components.
Areas Covered in the Session :
- This webinar explains how to choose and justify a sample-size for Lots that are included in Process Validation studies. The statistical methods discussed during the webinar include the following:
- Confidence intervals
- Confidence / Reliability Calculations (for variables & attributes)
- It then explains how to analyze those samples in such a way that they provide statistically valid final %Reliability for the production Process itself. One example is worked through completely.
Topics include:
- Introduction:
- Regulatory requirements
- Basic concepts and vocabulary
- Calculation of Sample Size to be taken from each Lot in the Validation study
- Calculation of % Confidence and %Reliability ( = %-in-specification) for each Lot
- Calculation of % confidence and %Reliability for the Production Process
- Worked example (with all calculations)
- Example summary “justification” statement
- Access to instructor’s website, for downloading free relevant statistical software
Who Should Attend:
- Research and Development Departments
- Quality Assurance Departments
- Quality Control Departments
- Manufacturing Departments
- Engineering Departments
Course Director: JOHN N. ZORICH
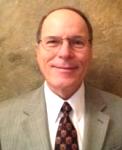 | John Zorich has spent 35 years in the medical device manufacturing industry; the first 20 years were as a “regular” employee in the areas of R&D, Manufacturing, QA/QC, and Regulatory; the last 15 years were as consultant in the areas of QA/QC and Statistics. His consulting clients in the area of statistics have included numerous start-ups as well as large corporations such as Boston Scientific, Novellus, and Siemens Medical. His experience as an instructor in statistics includes having given 3-day workshop/seminars for the past several years at Ohlone College (San Jose CA), 1-day training workshops in SPC for Silicon Valley Polytechnic Institute (San Jose CA) for several years, several 3-day courses for ASQ Biomedical, numerous seminars at ASQ meetings and conferences, and half-day seminars for numerous private clients. He creates and sells formally-validated statistical application spreadsheets that have been purchased by more than 75 companies, world-wide
|
|
|
|